Dresdner Combibord
Dresdner Combibord – der bequeme Einstieg
- Haltestellenbord für Bus und Bahn
- Patent-Nr. EP0892112A1
Mit der Einführung von niederflurigen Straßenbahnen und Bussen schuf die Fahrzeugindustrie die Voraussetzung für einen niveaugleichen Einstieg.
Das erforderte eine bautechnische Lösung für Haltestellen, die sowohl in Einzelnutzung als auch in kombinierter Nutzungsform von Bus und Bahn optimale Um- und Einsteigeverhältnisse schafft.
Der Dresdner Combibord berücksichtigt dabei die Anforderung an den bequemen Ein- und Ausstieg der einzelnen Nutzergruppen.
Er bietet Bussen die Möglichkeit, unmittelbar an die Bahnsteigkante heranzufahren, obwohl diese 230 mm über der Schienenoberkante liegt.
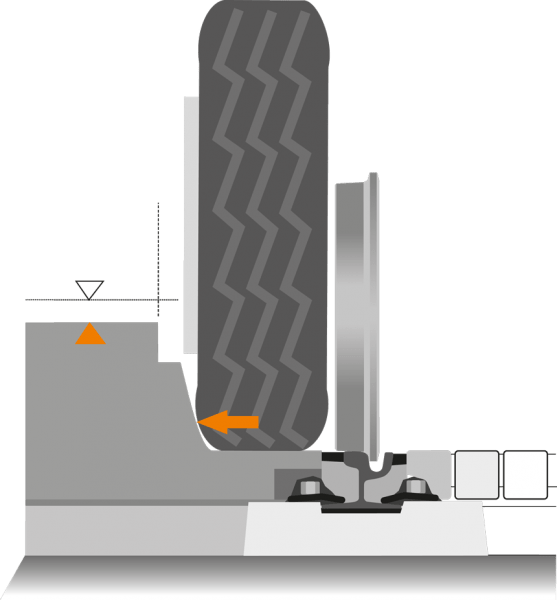
System, Material und Vorteile
Systemvoraussetzungen, die der Combibord erfüllt
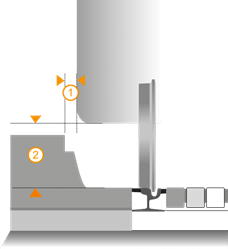
Straßenbahn
1. konstanter Abstand zum Bord
2. konstante Höhe zum Bord
Dresden: 29 cm über Oberkante Fahrbahn
Materialkomponenten des Dresdner Systems
Vorteile auf einen Blick
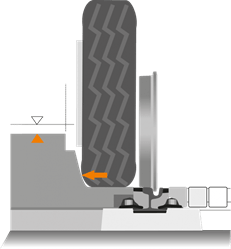
- kombinierte Anwendung für Straßenbahn und Bus
- ideale Führung des Rades durch Geometrie des Steines und kein Konflikt mit der Radnabe
- durch geringe Einstiegshöhe und Spaltbreite ist barrierefreie Nutzung der Fahrzeuge gegeben
- Aufnahme der hohen Anfahrkräfte
- keine Instabilität der Bordsteine durch Wirkung als Gesamtsystem
Verlegetechnologie
Anforderung an die Verlegung
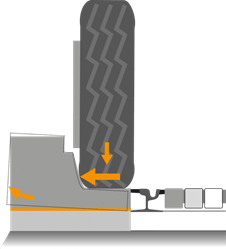
Durch starke Anfahrkräfte bei der Führung des Fahrzeuges Bus bei gleichzeitiger Belastung des Steines versagt die „klassische“ Bordverlegung.
Lösung: Verklebung des Bord auf bituminöser Tragschicht bzw. auf Beton
Testergebnisse mineralischer Kleber auf:
- bituminöser Tragschicht: 59 kN*1)
- auf Beton: 138 kN*2)
*1) Tragschicht mit Bord aus der Konstruktion gerissen
*2) Bord vom Untergussbeton abgeschert (Versuch 04/2010)
Qualitätssicherung
1 Anlieferung auf der Baustelle
2 Vorbereitung der Betonoberfläche
3 Vorbereitung Verlegung
4 Verlegung und Justieren
5 Vergießen mit Vergussbeton Pagel V1®/50
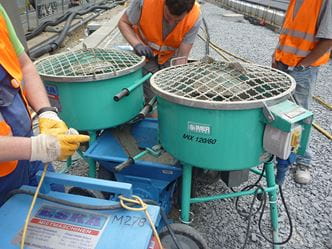
Das Anmischen des Vergussbetons, sowie dessen Förderung erfolgt auf der Baustelle maschinell mittels Zwangsmischer und Förderpumpe.